

An Agitator Conditioner Feeder, with secondary trough conditioning screw for semi-free flowing materials. A Standard Feeder, with static hopper, trough and feed screw for free-flowing materials.

The filter algorithms in the load cells or the platform scale effectively filter out vibrations, thus guaranteeing an exact weight signal at all times – even when the ActiFlow’s bulk material activation is at its maximum. Modular Design The Vibra Screw VersiFeeder is the first volumetric feeder with modular design, enabling a single unit to adapt to the broadest range of feeding applications. The ActiFlow control module constantly communicates with the KCM feeder control to ensure an ideal material flow in the hopper and maintain a very high feeding accuracy. The smart flow aid device applies gentle vibrations to the hopper wall, hereby carefully activating the contained material with the optimal amplitude and frequency. The ActiFlow TM system overcomes the disadvantages of a vertical agitator. Although this system is dependable, it requires additional headroom above the feeder, and cleaning is awkward, laborious and time consuming.
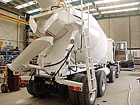
This is important in the design of hoppers, since for mass flow. Regardless of material flow characteristics, the NBE paddle-style or ribbon-style agitator eliminates material bridging and ratholing. In some instruments, the vertical force on the agitator can also be directly measured. Vertical agitators can be used to prevent ratholing and bridging of bulk material. NBE agitator hoppers are engineered with an internal mechanical agitator to ensure a consistent, reliable material supply is drawn toward the hopper discharge. Since bridges lack even the vertical tunnel of a rat hole, the material flow tends to be completely blocked. Material bridges similarly restrict the flow of material. Although material can continue to flow through the hole, the discharge rate of the feeder is lowered considerably and bulk material may deposit in the hopper. A rat hole is a narrow vertical tunnel from the top of the material bed in the hopper to the discharge device of the feeder. Such poor flow properties can lead to the formation of rat holes or even material bridges, making it difficult to accurately deliver these materials to the process. The following instrumentation can be found. Depending on the technology chosen, the mixer will discharge is a hopper that will be entirely connected to the mixer bomb doors, flap valves or that be connected through a short pipe to the mixer (round valve) Instrumentation. Detail fabrication drawing preparation was started based on the priority given by the client and completed in 35 days for all hoppers.Many bulk materials, especially fine powder, are cohesive and do not flow consistently out of the supply hopper during feeding. Some manufacturers have adapted their ribbon blender design by changing the agitator through the use of paddles or plows. After design approval the sheet was corrected for small changes requested from the client. Critical Requirement Sheet preparation for procurement was started after design submission and floated for inquiry. GA drawing was prepared based on design output and submitted for approval within one month for all the hoppers.
HOPPER AGITATOR DESIGN INSTALL
KAY APSC & KAY-5 Sanitizer/Cleaner Place a bucket b 8 Install agitator paddle.
HOPPER AGITATOR DESIGN SOFTWARE
Design for circular hoppers was performed using PV-Elite software for non-circular hoppers in-house developed excel sheet was used. Agitator paddle Hopper cover Milkshake cup holder Milkshake restrictor cap Drip tray Splash shield Syrup hole plugs Spout cap Spout cap o-ring Place the restrictor cap, splash shield, drip tray, and shake cup holder on a clean, dry surface to air dry overnight or until the heat treatment cycle is complete. The end client for this project was from the FMCG industry, so deliverables were required at an incredible pace. The shaft 4 is connected with the pneumatic cylinder 6 through a rack.

In the middle conical section at the bottom 2 and top 3 of the spacers is located shaft 4 with the blades 5. The middle part is made conical, it is the mixing of components, and the lower part of the cylindrical discharge. Design and Detail fabrication drawing preparation for 42 nos Circular and Rectangular hoppers as per ASME SEC VIII Div 1 and Good engineering practice.ġ) Design of 28 circular hoppers as per ASME SEC VIII Div 1 and Good engineering practice.Ģ) Design of 14 rectangular hoppers as per Good engineering practice and FEA for few parts.ģ) Detail Fabrication drawing preparation.Ĥ) Critical Requirement Sheet for procurement. Hopper agitator includes a housing 1, the upper part of which is cylindrical and serves as a hopper.
